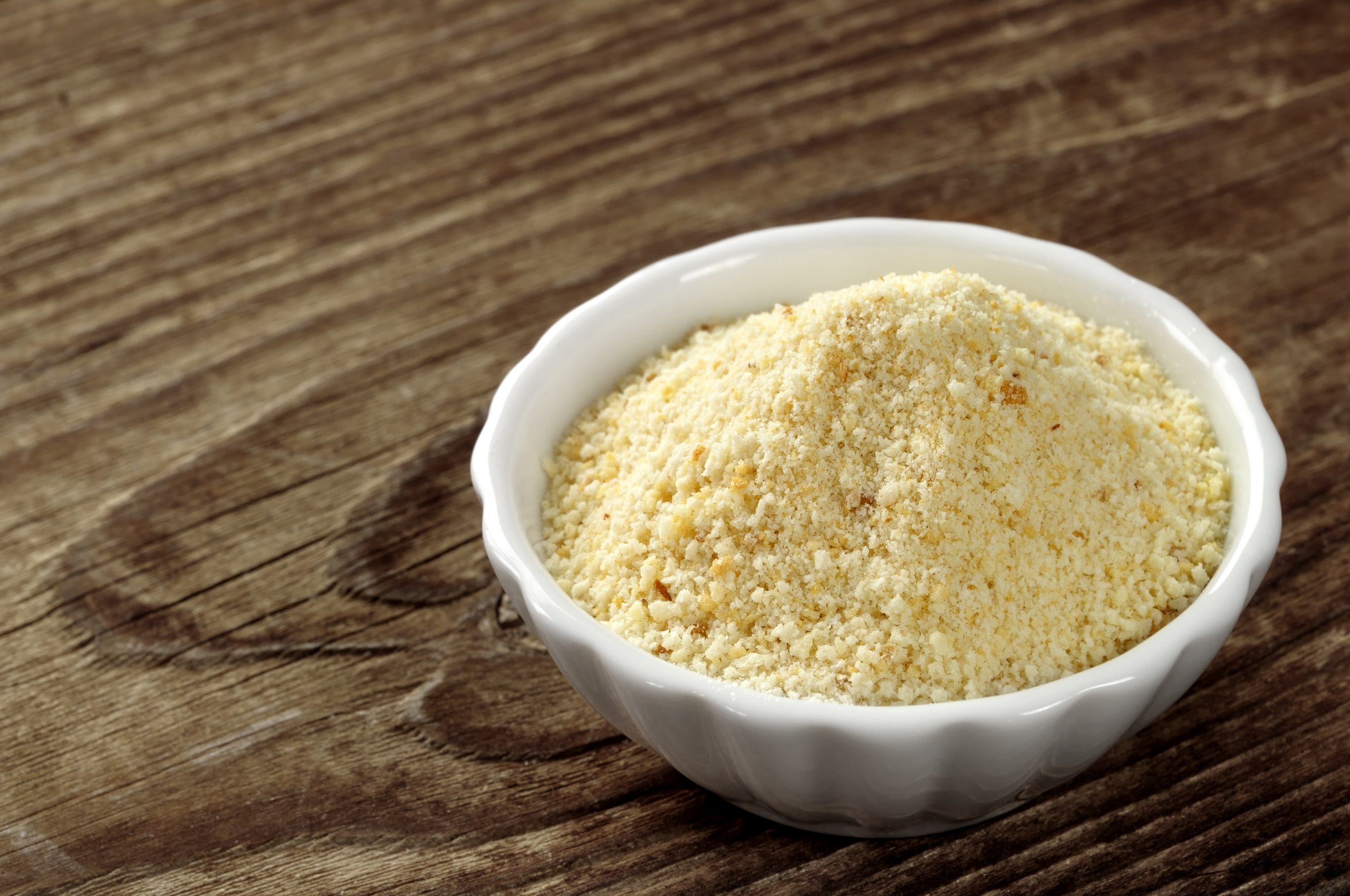
Manufactured crumb and its many benefits
August 20, 2019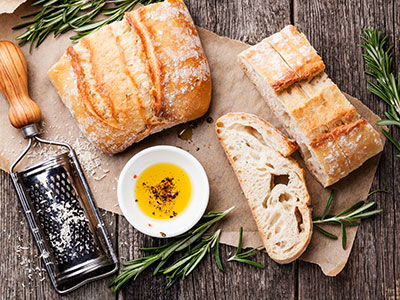
Ciabatta
September 25, 2019Lean manufacturing: How it can apply to your business
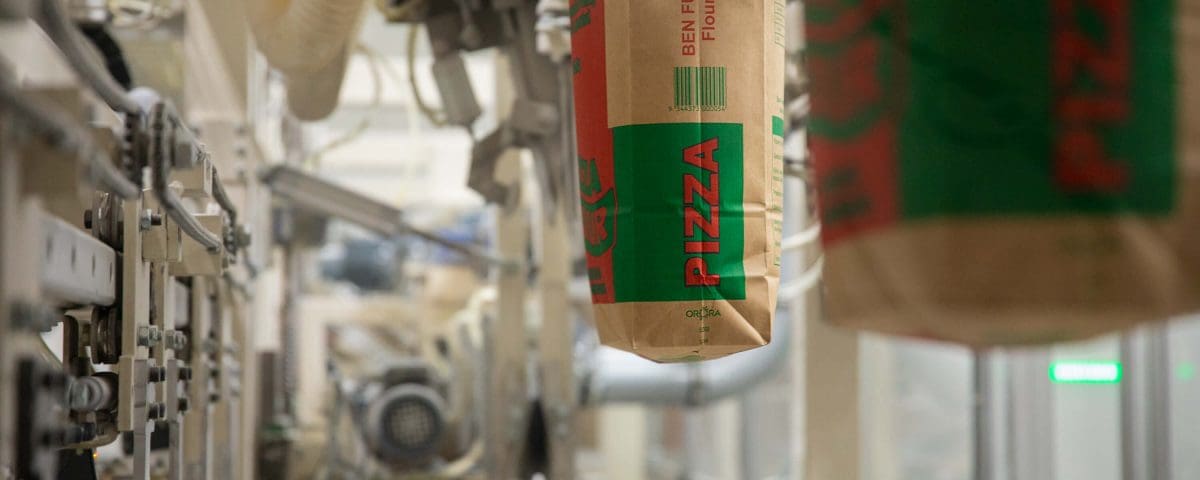
Ever wondered what the term ‘lean manufacturing’ means, how it works, and how it could apply to your business?
Good news – it can. The principles of Lean Manufacturing can be applied to businesses of all shapes and sizes, why? At its core, there are two simple words that everyone needs to pay attention to.
Eliminate and Waste.
Lean manufacturing is a set of processes and tools that eliminates waste from production. When implemented correctly, it can improve the efficiency and quality of your product, which generally leads to an increase in profit.
While making more money is obviously a key goal for many businesses, one of the reasons we use these principles, is that it enables continuous improvement.
At Ben Furney Flour Mills, it means we are always getting the best quality product to the customer efficiently. By levelling our schedule, we are able to simplify our ordering process, increase capacity and believe it or not, have improved our production output by 40%, with no infrastructure spend.
We will go into that later but first let’s talk about how it can apply to your business.
Types of waste
In the “Lean Manufacturing” world, it is believed that there are seven key types of waste to be avoided in your business.
At Ben Furney, we believe there is another key area of waste – unused skills of employees. If you’ve got someone who is multi talented pigeonholed into an isolated position – give them more responsibilities! If you’ve got as highly qualified staff member doing an entry level job, how can you better utilise them?
The 8 Wastes
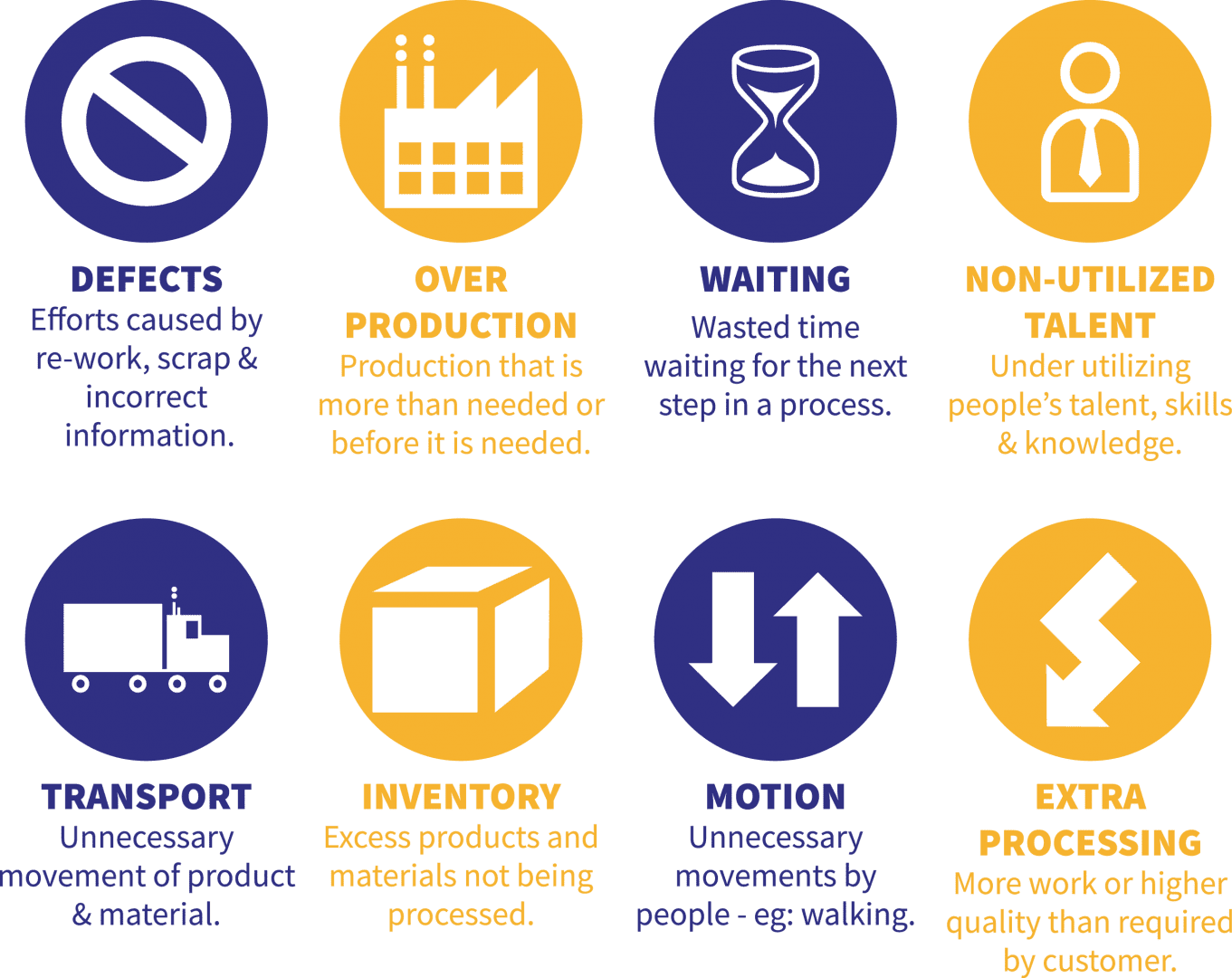
How to implement
If you are wondering what key areas of waste are and feeling overwhelmed about where to start, the first step is an audit.
This means going through all your processes, talking to employees and potentially getting a new perspective. Utilise any external resources at hand to identify your priorities and research and gain value from other resources.
Once you have established key focus areas, start with the key priority, where is the most waste occurring? Identify something you are doing all daily that is not being done efficiently, that is a priority. Work your way through, then move on to the next step.
The single most important step in this process is to consult with your team. People are often resistant to outside attempts to implement change, a process built from a team has a better chance of success.
Economies of repetition
These involve creating a situation where natural human behaviors that help to improve performance can flourish.
Repeating schedule
When people do the same task repeatedly, they get better at it. It’s a great way to train new staff and it’s a great way to keep production on track, consistently.
Routines
People live by routines. They like the stability, security, and predictability. It allows people to know what is expected of them – and how they can rely on others.
Regularity
Without standardization you can’t generate sustainable improvement. It is really difficult to achieve standard work when short term changes are frequent and the plan changes from week to week.
At the Forefront
We used the Economies of Repetition to completely level our schedule. This allowed us to
- Decrease overtime by 98% across the entire company
- Create additional 40% production capacity
- Increase tonnes per production hour on packing lines by 25% – through longer production runs
- Reduce Machine Down Time to under 5% by fewer and more efficient change overs
- DIFOT – Delivery In Full, On Time consistently sitting at 99.8% YTD
- Achieve 100% product to Specification YTD
Alongside all these wonderful figures, it also opened up our schedule for emergencies, or large ‘one off‘ orders. It has given us the flexibility and capacity to supply all the needs of our customers.
Which is a true reflection of the Ben Furney Flour Mills key accountabilities!